In-line Sensor for Structured Wire
Structured Wire (SW) is an evolutionary wire technology that can significantly increase wafering productivity due to more efficient transport of slurry and faster cut rate. One of the challenges to utilize an advanced SW technology is the need to track, in real-time, the physical SW parameters: bend amplitudes and periods. In-line Structured Wire Sensor is a new inspection system developed by Ultrasonic Technologies (UST) which allows automatic in-line measurements of SW characteristics before or during cutting of ingots. Following are the major specifications of SW Sensor:
- Maximum SW velocity: 13m/sec
- Accuracy of two SW periods: 10 microns
- Accuracy of two SW amplitudes: 5% st.dev. of amplitude
- Minimum SW base for data collection: 50cm
- SW length: >120km
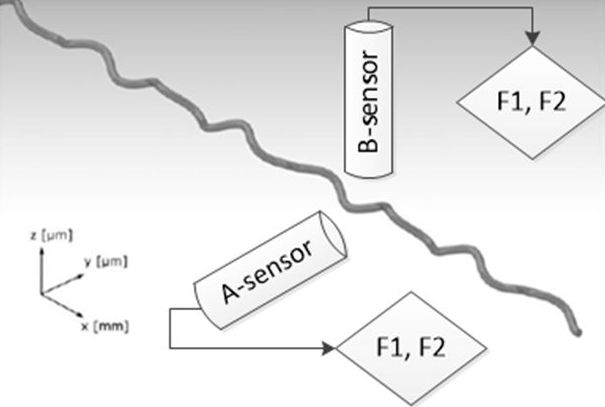
Diamond Wire Wear Inspection
The Resonance Vibrations (RV) method was developed for non-destructive real-time inspection of Diamond Wire (DW) quality. A theoretical model of RV in moving strings was developed. The in-line RV-DW sensor induces small vibrations in elastic DW segments during the wire motion in a wafer cutting tool and measures its resonance characteristics to assess wire quality and DW wearing stage. Core elements of the RV-DW sensor include a non-contact actuator and probe. The RV data acquisition and analyses are performed within tens of milliseconds, matching the speed of the modern wafering process. The RV-DW sensor is computer-controlled with Windows-based software and convenient Graphical User Interface.
RV vs. Optical
Wafer producers are exploring a high-resolution optical imaging to assess DW quality by detecting loss of material and tracking the DW wearing stage.
Optical method disadvantages:
- Only surface diagnostics of the wire components, while the DW wearing is also affected by degraded sub-surface layers (Ni, Cu.)
- The algorithm for real-time DW optical inspection generates high uncertainties caused by irregularities in the diamond particles.
- Silicon wafering creates chemical residues that requires frequent maintenance of the optical hardware.
RV-DW senor:
- Ensures inspection of the DW bulk and surface properties (both diamond particle loss and sub-surface metallization) during wafering.
- Reduces scrap material by eliminating DW breakage which leads to yield reduction and product cost increase.
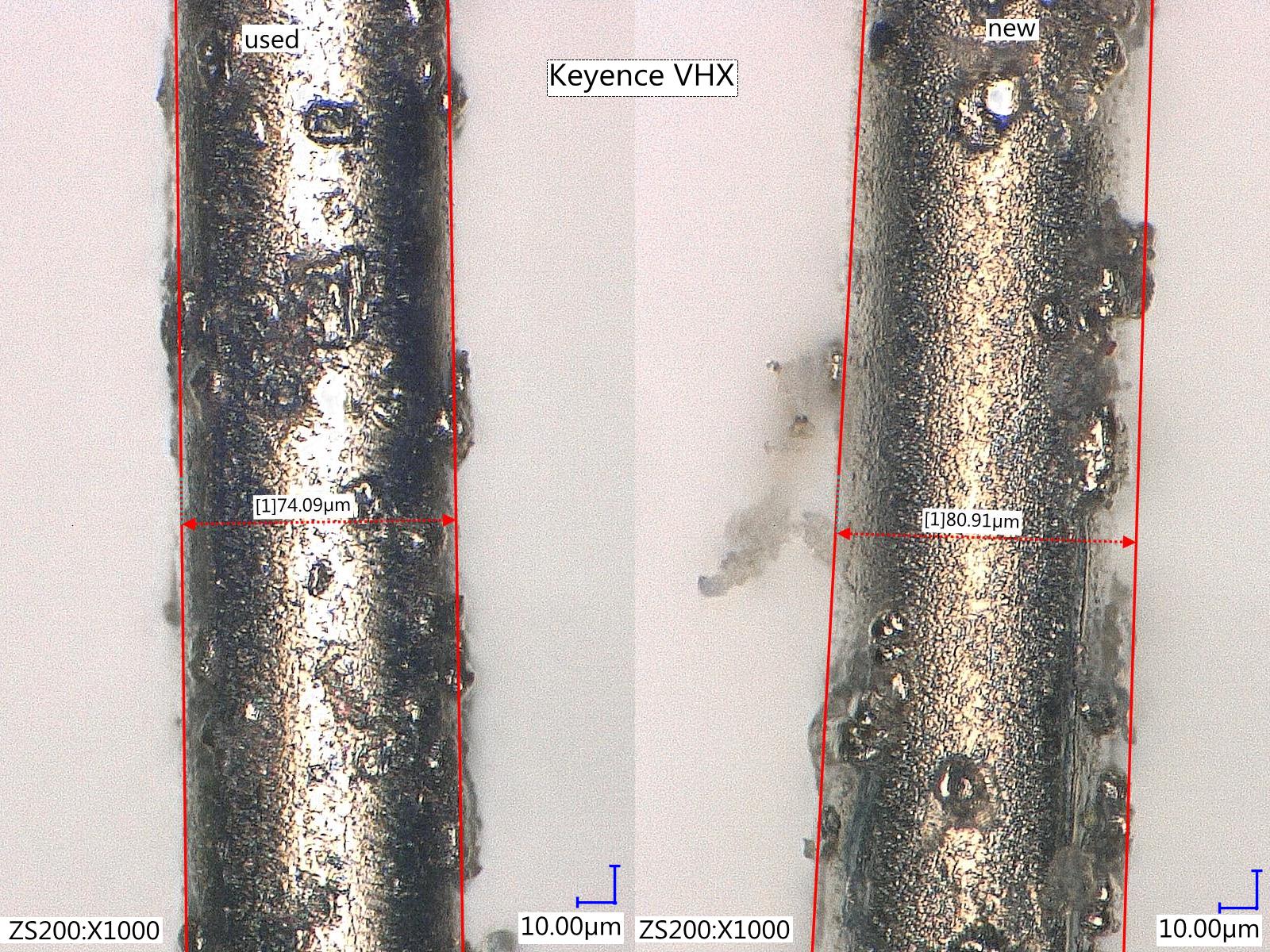
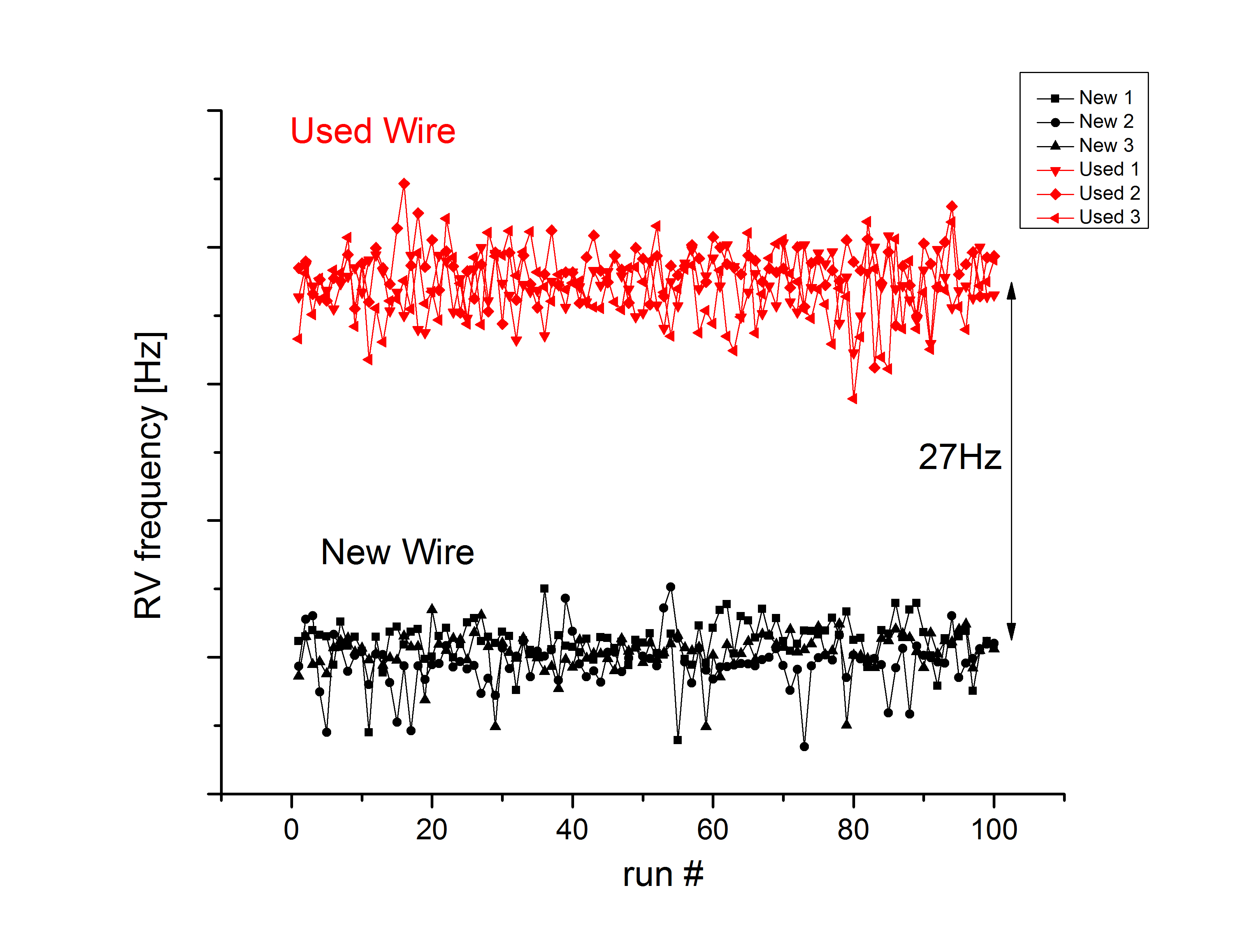
In pictures we show microscopic images (Keyence, VHX-6000) of new and used DW samples and data of in-line RV inspection. RV-DW sensor shows a clear shift of the resonance frequency between two wires.
RV Sensor Specifications
- Minimum diamond wire diameter - 60 microns
- Maximum DW speed - 30 meters per second
- Maximum temperature – 60C
- Accuracy of diamond wire wear – 10%
Additional details are available in the publications section.